
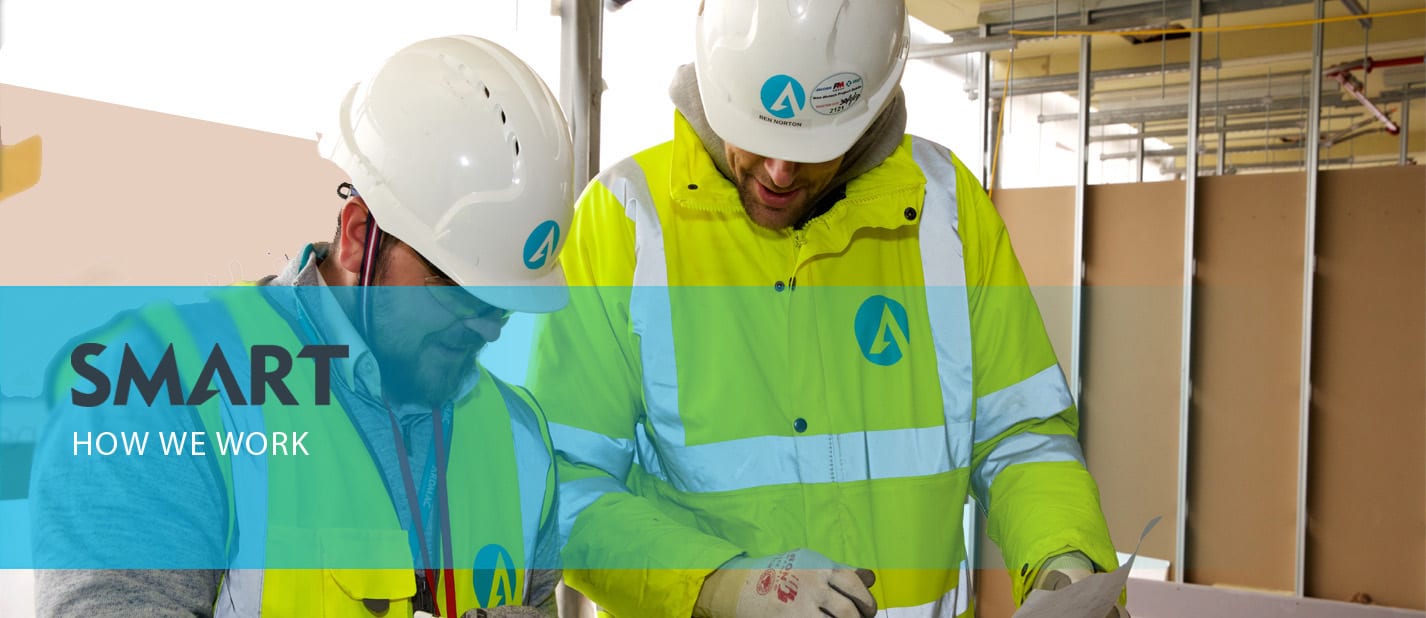
Working smarter, building better
We implement the latest, proven technology to improve processes that add value to our customers, improve efficiencies, and solve industry specific problems. The Ardmac Digital Construction Team is at the forefront of innovation, constantly exploring how the latest tools, software applications, and hardware can be deployed to support and enhance the work of our project and field teams.
Designed and executed on a collaborative digital platform that maximises the efficiency of all site activities our Building Programme combines the three pillars of LEAN Construction, BIM and Field Management which also involves proven methods to ‘design out’ all forms of waste from our
projects.
The route to higher efficiency
Although construction related attributes to 13% of global GDP, annual improvement in productivity has only increased by 1% in the past two decades (ref. McKinsey Global 2017).
Other key industries, such as manufacturing show 3.6% increased productivity.
This clearly indicates that our industry needs to change the way of working.
At Ardmac we have always embraced change and continuous improvement. This page of our website provides you with a summary of how we work.
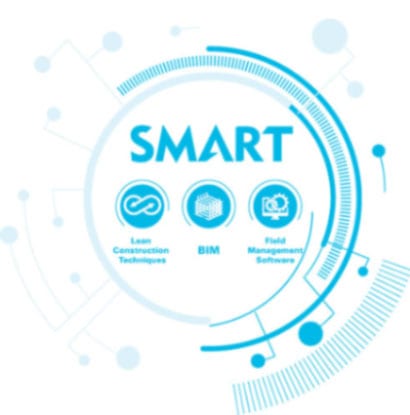
Mastering LEAN Construction
LPS® – The digital ‘sticky wall’ for better scheduling accuracy of your project
Last Planner® System (LPS® ) is an excellent entry point to LEAN. It is easy to understand and focuses on collaboration and cooperation.
It is a realistic way to collaboratively manage project-based production. As the name suggests, the LPS® systems engages last planners – the people ultimately responsible for getting the work done – in the planning and efficient execution of a project.
LPS® is designed to produce predictable work flow and rapid learning in programming, design, construction and commissioning of projects. Ardmac have successfully adopted LPS® on every project, small or large since 2018, and we have seen excellent results from this.
The benefits of LPS® include:
• Build trust & relationships among all stakeholders
• Build trust & relationships among all stakeholders
• Collaborative approach
• Eliminate waste
• Facilitate rapid learning curve
• Safety & Quality Audits & reduced Incidents & Defects
• Greater utilisation of resources
Other areas covered by our systems include:
• Identifies real constraints early (At 6 week look ahead)
• Improved ‘Value’ for client
• Predictable workflow
• Reliable activity tracking
• Root cause of issues reviewed (At daily huddle)
• Shorten project delivery
• Greater schedule certainty
Last Planner® allows the proactive sequencing of works and setting out productivity targets. At Ardmac we then link LPS® to our other systems to observe more efficiencies:
• LPS®Generate reports for payroll directly from bio-metric / facial recognition devices
• Eliminate individuals arriving on site (unannounced /without necessary paperwork) is a significant time saving benefit
• Reduction of administration time associated with on-site management on site
• Digital time and attendance systems
• Digitalisation of different credentials, providing notification to worker and management contractor in advance of renewal time
• Linking the deployment software to our field management platform has many benefits incl. allowing us to update the site daily diary automatically
Using LPS® allows works to be planned effectively, removes constraints ahead of time and enables management to focus on productively delivering projects. By monitoring field productivity daily, variances can be tracked. LPS®provides the facility to categorise these variances and thus identify trends.
Field Management & Productivity
Safe Deployment of labour on every project
Managing labour on a project can be a significant challenge using traditional processes. Paper-based documentation takes significant administration time, is prone to human error and can result in downtime which could have otherwise been used productively.
There is of course a need for a site tour and familiarisation meeting with all new starts upon arrival, but the time is now greatly reduced as all paperwork is completed online. It can be spent focusing on the crucial safety messages for the project rather than on scanning paper certs, logging details and taking photographs. This process is equally effective for management, direct employees and sub-contractors.
Ardmac successfully uses cloud-based linked real-time systems for all their projects. They provide management with crucial immediate records of who is on site, the workers safe deployment to the work force and their productivity.
Armed with this knowledge (on any mobile device) managers can devote more time to making decisions and being in the field supporting the project and less time at their laptops inputting data or reviewing spreadsheets that are immediately outdated.
A new start on site will receive a link to an online induction for both safety and quality that are site specific in advance of their start date.
To complete the induction, all essential credentials are first uploaded by the inductee.
These can include Safe Pass (Ireland), CCS (UK), Manual Handling, plant & machinery certificates of training and other relevant safety information pertinent to each worker. This greatly reduces the risk of people working on site without the correct and up to date credentials.
Part of the induction process is to read and sign any specific Risk Assessment, Method Statements (RAMS) relative to their role.
After successful completion of the induction and signing of the RAMS, the operative is issued an individual QR code that clears them to attend site.
The use of QR codes facilitate the efficient keeping of safety records for all works.
Building Information Modelling (BIM)
Ardmac have been delivering projects through BIM for over 10 years.
At first this started with the generation of 3d models for
co-ordination and clash detection purposes.
Overtime through experience and extensive training, capability to implement BIM was increased on projects including highly detailed, information rich 3D models up to LOD500.
Ardmac have 29 BIM resources and recently achieved ISO 19650-2 Certification with BRE which demonstrates both commitment to BIM excellence and ability to deliver projects using BIM.
Other ECI tools at Ardmac – Adding value at design, development and construction stage
Complex building projects crucially require detailed expertise at an early stage to influence the facility design.
This page of our website explains how Ardmac as specialist contractor engages at an early design stage of a project (ECI) to form part of a multidisciplinary design team.
Cloud-based collaboration is enabling design teams to work together remotely from different locations.
Ardmac works with a wide range of advanced construction systems and applications:
Ardmac works with a wide range of advanced construction systems and applications:
Autodesk products such as Revit:
Design, model generation and layout drafting.
Navisworks Manage:
Co-ordination with other trades and clash detection as shown above.
BIM360:
Storage of project models / Cloud-based co-authoring of model files.
DFMA:
Generate detailed 3d models, allowing for the classification and
quantification of materials directly from the model, which can then be
transferred digitally to manufacturing partners production software.
Anything that is modelled, is coded. Schedules of quantities and sizes
(or any other properties) that are linked to model objects can be extracted with ease.
BIM on site:
Model viewer software for tablets allows you to bring the project model into the field so that teams can now review issues on site.
BIM for Planning (4D BIM):
Detailed object data is also transferred which allows users to select and interrogate objects:
• Project models can be linked to the project schedule using Syncro.
This allows the visual review of the project plan and identification of
any potential sequence clashes with other trades.
• Clients are better able to understand the sequence of works by reviewing the animations while the system can also be extremely effective for site
logistics as well as construction activity planning.